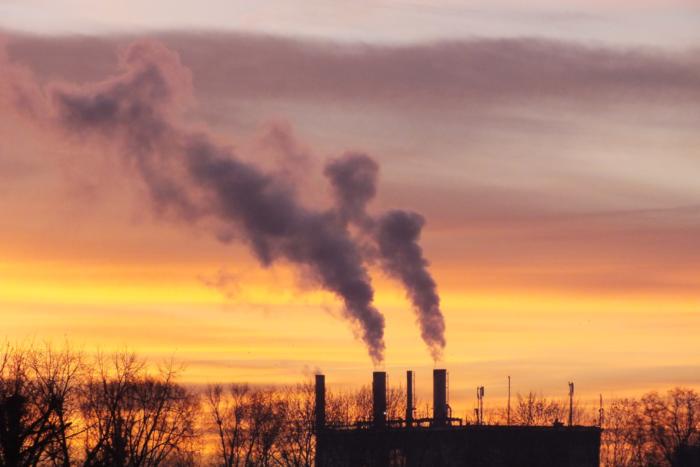
Details
Solution type
In general, optimisation is about finding the best available values given certain limitations and functions. All processes and systems, such as a district heating system, can be optimised to achieve the best possible values, based on predetermined settings.
District heating and cooling systems can be optimised in several ways, from optimum substations to larger system optimisations, all important in their own way. This can for example be about how to prioritise and run different plants and boilers, if a system consists of such, depending on the heat and cooling demand. In general, what is important in all optimisations is that a well optimised system can bring financial benefits. It is always good to regularly assess and evaluate the installations that have been made to improve the systems, which will in the end lead to savings. Other benefits could be for example better routines, safer working environments for staff and environmental benefits. The market for decentralised energy is more mature in some European countries than others. In order to optimise production and supply chain costs, full procurement exercises could be conducted to drive competition within the relatively small field of manufacturers.
Assets
This section is about the order in which different production units are used in a district heating system to obtain the best financial outcome. Figure 1 is a schematic duration diagram illustrating which production units are used depending on the outdoor temperature. In this case, the order of priority depends on the cost of production; which in turn depends on fuel prices, electricity prices, taxes, policy instruments and maintenance, repair and operation costs. The order will vary depending on how these settings are varying. If the district heating and cooling company have well developed economic optimisation routines, there will be guaranteed benefits, such as financial savings.
Figure 1. Schematic duration diagram illustrating which production units are being used depending on the outdoor temperature.
Effective optimisation requires a clear understanding of the system's objectives. Good mathematical modelling in turn benefits from effective IT systems. The model needs to be populated with high quality data; usually a mixture of observational data, data from formal experiments and expert judgement from stakeholders. Some concluding remarks. For the best possible accurate optimisation, it is important to…
- … regularly assess and evaluate the installations that have been made to find possible improvements
- … manage obtaining the correct information at any given moment (data management, clear agreements, good relations with counterparts etc.)
- … have good internal and external Collaborations
- … have good IT Systems and Models
- … have good Risk and Scenario Management
Optimisation Process
There are several ways to optimise the order of production units, based on economic perspectives. Figure 2 presents one economic overview [EUR/MWh] of how the local energy company Göteborg Energi in Gothenburg, Sweden optimises their order of production units in a district heating- and cooling system (at the time of writing). The order of production is based on the heating and cooling demand per set time unit, for example [MW/h] or [MW/min].
Figure 2: Example of an optimisation process regarding finding the best possible order of production units to meet the heating and cooling demand.
The first step is to create a prediction of the heating and cooling demand. It can be beneficial to use a load forecasting system which utilises weather forecasts, and possibly historical data (statistics on likely heat demand on a given date and time) as well. The calculated heat demand needs to be handled in some way, for example by using an operation management system to store the data. To conduct the main optimisations some kind of software is required. One option is to use linear programming and conduct iterations. Based on the heating and cooling demand the demand will be “filled up” with the cheapest production unit [EUR/MWh] and then added onto other production units to meet the demand. The software/model needs to be fed with input data and “boundary conditions”, such as functions and limitations, and also in some cases be compatible with interfaces to other systems. Input data in this process are:
- The heating and cooling demand
- Available facilities and their effects (Some plants might have technical issues which reduce their maximum and minimum effects.)
- Available fuels (There might exist logistical problems that will lead to limitations in how the facilities can be run.)
- Costs, e.g. fuel prices, electricity prices, taxes, policy instruments and repair and operation costs
The “boundary conditions” could be technical limitations in the district heating and cooling systems as well as agreements (for example agreements with energy markets, such as the power and gas markets, and agreed monthly delivery effects from excess heat companies and/or other energy companies). The results from the optimisations can be presented in different ways. Figure 3 shows an example of how the result for “heat demand in Gothenburg, Sweden” can be graphically presented. The y-axis to the left side indicates heat demand [MW], the y-axis to the right side shows the outside temperature [ºC] and the x-axis displays time [h]. Note that the blacktop curve is the total heat demand in the system and that the “layers” below symbolize different production units, starting with the cheapest at the bottom (also called the base load). For Gothenburg, the base load consists of heat from the waste incineration plant and excess heat from the refineries, along with excess heat from the adjacent connected municipality of Mölndal. The blue line indicates the outside temperature. The solid lines are the temperature outcomes and the production outcome, and the dotted lines indicate the temperature forecasts and the production plan.
Figure 3. Example of a graphical presentation of how the heat demand varies depending on the time of the day.
It could be of value to have different “Production Plans” with different time horizons, which can be used for different purposes. The “Production Plan, 1h – to 4 days” from Figure 2 above is used to decide how to prioritise the plants in the short term, where it is required to make quick decisions depending on quick changes and unforeseen events. The production plan also consists of calculated fuel demands and is also used as material for decisions regarding suborders on fuels; such as wood, pellets, electricity and natural gas; that need to be ordered on short notice. The “Production Plan, 5 days – 6 weeks” is mainly used as a discussion material in order to plan necessary production stops in specific facilities and as a trading material on the financial market, along with making agreements with other external parties and firms (e.g. long term contracts with biofuel companies and excess heat companies). Production Plans that have a longer time horizon than 6 weeks could be beneficial from the perspective of for example financial planning and risk and scenario management. It is an advantage if the optimisation process can be frequently repeated to adapt to changing external conditions and model improvements. Monitoring of the outcome compared to the forecasts/prognosis and plans is a key factor in order to constantly improve the optimisations (models, routines, outcome, costs). Examples of monitoring factors are:
- Actual production costs per time unit compared to calculated optimal production costs per time unit. The unit could be called “additional costs” [e.g. EUR, EUR/MW].
- Additional costs for each plant [EUR]. This could help to prioritise which plant should be given priority to be upgraded.
- How well each plant was run compared to its optimal maximum effect [%].
- Emissions [e.g. CO2/MW].
Risks and applied solutions
Models might never correspond precisely to reality. Moreover, results need to be interpreted and communicated to decision makers and other stakeholders, at the same time making uncertainties explicit. In this way, the decision makers can weigh the various risks against each other and make their decisions based on the current conditions. If there is a change in personnel it is important to forward the experience and knowledge from the personnel leaving, especially if the models are basic and are in need of more comprehensive interpretations and improvements.
Stakeholders
There are different stakeholders involved in an optimisation process, which could be both internal and external. An optimisation process could also consist of sub processes. For all these processes, good collaborations and good agreements between counterparts are key success factors.
Figure 4. Cooperation to achieve optimal operation.[/caption]
One example of an internal sub-process is illustrated in Figure 4, which shows how the operation centre cooperates with different internal stakeholders in order to achieve the optimal operation of the district heating and cooling system. The operation centre receives the production plans (time horizon 1h to 4 days) through the “Economic and Financial Control Department”, which regularly updates the plans on a predetermined frequency as well as on acute demand year-round. The operation centre uses these plans as input for decisions on how to run the system (e.g. which boilers to start/stop and the duration of this), and communicates regularly with other internal stakeholders; such as technicians, engineers, the environment and chemistry department and the repair and maintenance department. It is always important to have clear predetermined priorities and routines in place when unforeseen events occur. These are the general predetermined priorities for the operation centre at the local Swedish energy company Göteborg Energi at the time of writing:
Examples of collaborations between the local energy company Göteborg Energi and other external counterparts are:
- A waste incineration company
- Industrial excess heat companies
- Other nearby energy companies
- Other nearby municipalities
Finance
The main expenses when working with optimisation processes consist of staff time; such as programming time, regularly conducting the optimisations and interpreting the results. There might also be expenses for software licenses. The costs can be divided internally between the concerned departments. Before investing in any software, it can be valuable to weigh the expenses compared to the improved benefits. Sometimes Excel programming might be sufficient for the requested demand. Good optimisation processes often pay off with benefits such as financial savings, better routines, a safer working environment for staff and environmental benefits.